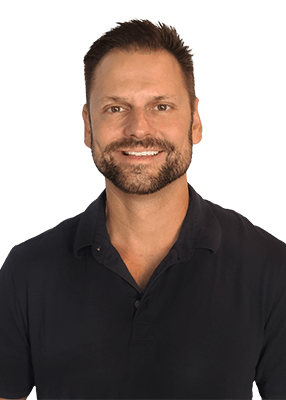
by Paul Wheaton
April 24, 2025
The construction estimating process is a critical component of construction, responsible for keeping projects on budget. All construction companies should have an in-depth understanding of how estimating works and why it is important.
Although cost estimating is crucial for profitable construction projects, it is still complex and often professionals may have a few questions. We’ve answered some of the biggest bidding questions to help anyone who wants clarity.
What is Construction Estimating?
Construction estimating, also referred to as construction cost estimating, is the process of mapping out all costs related to the scope of a project. This includes direct costs associated with materials, labor and equipment and indirect costs, such as overhead and insurance.
Through cost analysis, estimators can create a price estimate that can be used to bid on new projects.
Why is Construction Estimating Important?
Estimating is crucial for a construction project to be successful. From creating competitive cost estimates for winning bids on projects to finalizing budgetary closure at the end of construction, estimating plays an integral role.
According to a survey on construction costs, the average profit portion of builders for a project’s sales price is 11.0%, a relatively slim profit margin. This means that if cost calculations are incorrect by even a little bit, it could end up cutting into a contractor’s profit.
Calculating all project costs is also necessary to create a project budget, which acts as the roadmap to profitability. Any inaccuracies with estimation can lead to project overruns with potential forced cost-cutting.
How Are Estimates Created?
Here are the general steps for the cost estimating process:
- Review the project bid package provided by the client. The bid includes the project scope and timeline of work, which can be used to determine the material and equipment needed for the entire project.
- Visit the construction site to assess location conditions, such as environmental impacts.
- Quality takeoff, which uses the provided blueprints for measurements and calculations for all material, labor and equipment quantities.
- Cost analysis, which breaks down and prices all quantities for materials and equipment usage/mobility. Princes must be solicited from suppliers and compared to find the best options.
- Labor evaluation to break down the wages, taxes and overtime for required workers. Estimators must consider worker skill level, productivity on previous projects.
- Calculate insurance and bonds that are needed for the project. Contractors must be covered while working on a project and additional coverage must be factored in.
- Calculate overhead costs, or ‘indirect costs’ are calculated, including rent, utilities and permitting, which may not always be visible on original bid.
- Profit and contingency planning to see how much a project will earn a contractor. Contingency entails setting aside funds for unforeseen costs, typically 5-10% of the total project cost.
- Final submittal of the estimate as a bid proposal to the project client. At this point, the estimate will be thoroughly reviewed and checked for discrepancies. Once approved, it will be submitted to the client.
As you can see, the cost estimating and bidding process is long and complex. This necessary set of steps ensures that clients and contractors alike are benefiting financially, no matter the project size.
What Are The Methods of Estimating?
Estimating can be approached in a variety of ways. From looking at the big picture to focusing on accurate details, each method has its own benefits and drawbacks.
Determining the technique of estimating largely depends on how much time an estimator can spend on it and the level of detailed information they must work with.
These methods include:
- Analogous/Top-down estimating looks at the big picture, using historical data from similar projects to predict costs. This method is very fast but less accurate as it is only using general information.
- Detailed/Bottom-up estimating looks at the small details of a project and identifies costs for every item to create a full estimate. It is time-consuming but produces a very accurate project estimate.
- Parametric estimating uses statistical models of historical data and specific parameters to calculate costs. It is highly accurate but requires comprehensive data and construction estimating software.
- Assembly estimating separates each ‘system’ of construction (i.e. foundation, framing, roofing, etc.) and estimates costs for each individually and then is combined for the final project estimate. Although very accurate, it is time-consuming as each system must be calculated individually.
- Unit cost estimating is the most straightforward method, calculating costs based on the standard units of measurement (e.g. square foot, cubic yards, tons). It is useful for fast rough estimates but should not be used for large or complex projects, depending on the type of project.
- 3-point estimating creates a range of three possible outcomes for a project estimate: best guess, worst-case (pessimistic) and best-case scenario (optimistic). This range is useful for decision making but can still be subject to guessing.
What Factors Impact Cost Estimating The Most?
Even though the process of estimating involves many different moving parts, there are a few critical factors that make or break an effective cost estimate, impacting processing time, effort and cost.
An ambiguous project scope and unclear project requirements can make it difficult to create a solid cost estimate. The less concrete details an estimator knows about a project, the harder it will be to create an accurate project estimate that accounts for everything. This can lead to unforeseen additional costs later in the project.
Depending on how complex a project is, the cost may rise to meet required skill levels for estimators as well as the length in time and energy that they will have to spend.
The quality of data or the information used to create the estimate can lead to errors or omissions if the data is poor. Outdated data, such as old pricing for materials, can halt progress and raise costs for revised research.
The method of estimating can also greatly affect the estimating process. Some methods, like manual bidding, might be less accurate or detailed, making assumptions that could lead to increased costs.
What Are Some Common Mistakes When Cost Estimating?
Because the cost estimating process is so long and complicated, there is no shortage of opportunities for mistakes.
These are the most common construction estimating mistakes:
- Inaccurate labor costs
- Not including overhead costs
- Use of generic items or assemblies for specific trades
- Inaccurate pricing for materials and supplies
- No risk assessment
- Not creating contingencies, such as weather planning
Many of these mistakes can be avoided with estimating software, where the risk of human error through manual estimating and calculation is reduced.
How Can I Improve My Cost Estimating Accuracy?
There are a few steps you can take to improve your estimating accuracy, such as:
- Compare to similar projects to see where adjustments have been or need to be made.
- Get detailed quotes from different suppliers for better pricing options.
- Use detail-focused estimating methods, such as ‘bottom-up.’
- Update cost databases on a regular basis.
- Encourage communication and collaboration between roles and clients.
Additionally, while estimators should observe all these tips, the easiest and most effective way you can improve your construction cost estimating is by using construction estimating software.
What is The Benefit of Using Construction Estimating Software?
In today’s digital age, manual methods for tracking and recording information are impractical for keeping up with the speed and demand of the construction industry. With construction estimating software, every step of the estimating process is made more efficient and accurate.
Here’s how:
- Advanced automation helps reduce time spent on tasks like cost calculations, data entry and quantity takeoffs.
- All-in-one system is built to align estimating and takeoff, so contractors never have to double-input data.
- Access to trade-specific estimating databases, which promote fast and accurate estimates.
- Change order management helps keep projects running smoothly even when changes are needed.
- Detailed reporting on project estimates vs. real costs to help budgetary analysis.
- Integration with accounting software allows for seamless translation of financial information.
- Cloud access and storage for estimate viewing from any location.
All these features, combined under a streamlined software system, can be an invaluable tool for construction contractors, making it fast and easy for estimates to be completed and trusted.
Which Estimating Software Should I Use?
There are lots of construction software products on the market, but here are some tips for what you should keep an eye out for when selecting your estimating software.
An estimating software should have the core features needed for your work, such as trade-specific databases, automated reporting, change order management and built-in takeoff.
It should also have scalability to match your company’s workload and growth, as well as the ability to integrate with other systems, such as accounting.
Look for high-quality software support that can be accessed at any time, as well as training courses for software use.
Search for a provider that has a positive and reliable history in the construction industry.
Also consider:
- The type of work being performed
- What building codes are dealt with
- Your business growth plan
If an estimating provider is good, they will help ensure that the software works for you, building a strong relationship in the industry that can last indefinitely.
Ensure Accurate Project Costs With McCormick Construction Estimating Software
Because construction cost estimating is such a complex and drawn-out process, contractors may have many questions, but it is important that they are answered.
Construction estimating consists of identifying all necessary and potential costs related to any given project. It is important because it determines if a project is feasible and how a contractor should delegate resources.
Accuracy is critical for every step of estimating, but construction estimating software can help ensure accuracy that manual methods cannot, which will lead to more profitable projects.
Cost estimating software comes with a host of beneficial features that make estimating for any project simple and fast. While there are many options, consider McCormick for your construction estimating needs, with its best-in-industry service.
McCormick offers top-of-the-line features for the electrical, mechanical and plumbing trades, including:
- United all-in-one takeoff and estimating under a single platform
- Built-in change order management and tracking
- Design Estimating Pro – built-in digital takeoff
- Real-time supplier pricing reports and comparisons
To learn more, contact a specialist today!
Share Article