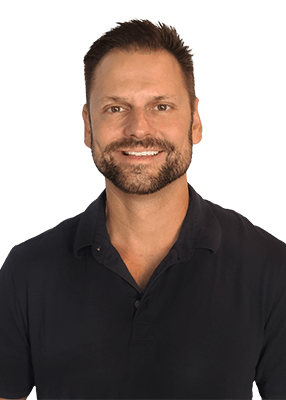
by Paul Wheaton
March 13, 2025
Many new or inexperienced contractors find themselves asking “What is a construction takeoff?” Even if you have worked in the industry for years, technology and bid requirements are constantly changing, affecting the takeoff process.
A construction takeoff is an important calculation that transforms blueprints and designs into a comprehensive list of required materials and related costs.
This is an essential first step in project estimation for construction. Takeoffs will be used to:
- Develop accurate budgets
- Determine precise material requirements
- Establish realistic project timelines
By accurately quantifying needed materials, estimators can provide clients with transparent, reliable cost projections. In turn, this builds trust and minimizes financial surprises during project execution.
Whether you’re new to construction or an experienced contractor, understanding takeoffs is important. Construction takeoffs provide invaluable insight into the intricate world of construction planning and cost management.
Construction Takeoff’s Key Takeaways
- A construction takeoff is a comprehensive calculation that transforms blueprints into a detailed list of required materials and associated costs.
- Takeoffs are crucial for developing accurate budgets, determining material requirements and establishing realistic project timelines.
- Construction takeoffs serve multiple purposes including material ordering, informing labor costs, determining equipment needs and guiding project scheduling.
- Advanced takeoff software offers significant advantages, including faster calculations, error reduction and improved estimation precision.
- Integrated, all-in-one takeoff and estimating platforms can reduce expenses, minimize data translation errors and enhance overall productivity.
Construction Takeoff: A Description
Construction takeoffs form the bedrock of project estimation. It is far more than a simple list of required materials.
At its core, a takeoff is a systematic breakdown of every component needed for construction. The list of materials and costs comes from architectural drawings, blueprints and specifications.
When creating a takeoff, estimators analyze construction documents for exact measurements and quantities. These measurements typically follow industry-standard units:
- Linear feet for materials like cable length and raceway systems
- Square feet for things like lighting coverage calculations
- Individual counts for fixtures and specialized components
Each trade requires distinct measurement approaches. For instance, electrical takeoffs focus on circuit lengths, fixture counts and power requirements. Plumbing takeoffs detail pipe runs, fixture counts and connection points.
But here’s where it gets tricky: takeoffs aren’t just calculations for materials needed. Estimators must also consider many things that impact material quantities including:
- The square footage of the area
- How many floors/levels must be factored in
A well-executed takeoff includes several key components:
- Detailed material lists with precise quantities
- Clear notation of measurement methods used
- Specific callouts for special or custom items
- Waste factor calculations
- Phase-specific material requirements
Additionally, thorough takeoffs document any assumptions made during the calculation process. Estimators make note of any uncertainties that may require clarification from architects or engineers.
These detailed analyses ultimately serve multiple purposes beyond simple material ordering. Takeoffs will also:
- Inform labor cost calculations
- Help determine equipment requirements
- Guide project scheduling
- Provide crucial documentation for change orders and project modifications.
When done correctly, construction takeoffs create a comprehensive framework for successful project execution and cost control.
Common Construction Takeoff Challenges
The problem is that construction takeoffs are complicated. And when they aren’t done correctly, the errors can cause major problems.
Common pitfalls often emerge during the takeoff process.
Inexperienced estimators might overlook crucial factors. For example, they might forget about material overlap requirements or fail to account for structural elements that affect material quantities.
Another frequent mistake is not considering phase-specific requirements. Temporary power needs during construction or scaffolding requirements for elevated work are two such examples.
Some estimators also make the error of using incorrect scale factors when working with digital plans, leading to significant quantity discrepancies.
Trade-specific considerations add another layer of complexity.
Mechanical takeoffs require a detailed understanding of ductwork and equipment specifications.
Electrical takeoffs must account for voltage drops over distance and load calculations.
Plumbing takeoffs need to consider pressure requirements and fixture unit calculations.
Each trade brings its own set of standards, codes and best practices that must be integrated into the takeoff process.
Importance of Construction Takeoffs
The strategic importance of construction takeoffs extends far beyond simple material counting, encompassing critical business outcomes as well.
1. Accurate Cost Estimation
Accurate estimations prevent expensive mistakes. If a contractor guesses wrong about materials, they could spend too much or too little.
For example, a wrong guess on a $500,000 project could mean losing $25,000. That’s a big deal for any business.
Takeoffs work by turning building plans into precise material lists. Estimators measure everything carefully, check current prices and calculate exact quantities. This means fewer surprises later and more accurate budget estimates.
2. Risk Mitigation
Comprehensive construction takeoffs serve as fundamental risk management tools.
Takeoffs identify exact material quantities and potential procurement challenges before building begins. This way, contractors can proactively address potential supply chain disruptions, material shortages and budget constraints.
The predictive capabilities of takeoffs allow for more strategic planning and reduce the likelihood of costly project delays or financial miscalculations.
3. Bidding Advantages
Construction firms that master precise takeoff techniques gain a significant competitive edge in the market.
Accurate, transparent cost estimates demonstrate professional expertise. It also builds client trust.
By presenting meticulously calculated material requirements and associated costs, contractors prove they are reliable and detail-oriented. They demonstrate that the business can deliver complex projects within budgetary constraints.
4. Financial Sustainability
Effective takeoffs contribute directly to a construction firm’s financial health, including:
- Preventing material waste
- Optimizing inventory management
- Supporting more accurate financial forecasting.
The ability to predict material needs with high precision allows companies to negotiate better pricing with suppliers. It also reduces excess inventory costs and maintains more consistent profit margins across multiple projects.
Why Construction Estimators Need Advanced Takeoff Software
Modern construction estimating demands precision, speed and efficiency. These are things that manual takeoff methods can’t do consistently.
Estimators deal with pressure from their bosses to produce accurate bids quickly, manage complex project details and stay competitive in the industry.
Construction takeoff software is the best solution for this problem. It improves the project estimating process. It also helps with time management and reduces errors.
For example, digital platforms enable instant area and volume calculations, providing near-instantaneous results that would take much longer through old methods.
Moreover, technology can cross-check dimensions and quantities to ensure accuracy in project estimates.
A Complete Solution
The best upgrade for estimators to make is investing in an all-in-one platform that combines takeoff and estimating functionalities.
Consolidating multiple software tools into a single comprehensive package allows companies to reduce expenses. Less hardware means lower initial investment, reduced maintenance costs and simplified IT management.
Beyond financial benefits, an integrated platform minimizes data translation errors because data is automatically shared instead of needing to be re-entered.
Using an all-in-one streamlined approach enhances productivity. It also provides a more reliable, consistent estimating process that gives construction firms a competitive edge.
Using McCormick For All Your Takeoff Needs
Construction takeoffs are critical. They help contractors plan for costs and quantities of needed materials for a job.
By systematically measuring and counting required materials, contractors can develop accurate project budgets, minimize financial risks and optimize resource allocation.
Digital software solutions are revolutionizing the estimation process. It enhances accuracy, efficiency and competitive bidding capabilities.
McCormick is cutting-edge electrical, plumbing and mechanical software that sets the industry standard. It enables tradesmen to streamline their estimation processes.
By leveraging McCormick’s estimating software, construction professionals can:
- Reduce manual calculation time
- Minimize material waste
- Generate more competitive project bids
With McCormick, you’re not just getting a software solution. Contractors are gaining a technology-driven ally committed to your project’s financial success.
To learn more, talk to a specialist today!
Share Article